1970年操業開始。約28万平米の広大な敷地に3つの工場のみならず、商品開発センターや研究所を擁するダイキンの中枢工場である。
ダイキンは1924年に大阪金属工業所として創業。1963年に大(ダイ)と金(キン)をとったダイキン工業に改名した。同社の柱である空調事業の売上高は約9400億円。米国のキャリア社(コネチカット州)を抜いて、世界一となった。ちなみに、同社は化学品にも強く、フッ素化学製品は米国のデュポンに次いで、世界2位にシェアを有している。
空調分野ではもともとビル用などの業務用に強みを持っていたが、家庭用でも力をつけ、加湿機能と除湿機能の両方を兼ね備えたルームエアコン「うるるとさらら」のヒットなどで、国内ではパナソニックに次ぐ2位のシェアを確保している。
滋賀製作所で生産している製品は、主に国内向けの高級機種。リーマンショック前には年間約160万台生産していたが、現在は100万台程度。提携している中国・格力電器へ普及品を生産移管していることもあり、生産台数は減少傾向にある。
しかし、滋賀製作所の真骨頂は、生産規模ではない。一口に100万台といっても、それを構成する機種数はなんと250。1日に生産する機種のバラエティだけでも、100種類を超えるという。これだけの機種を、段取り替えなしで、いかに効率的に生産するかが工場の腕の見せ所である。
しかも、空調機器は需要の季節変動がきわめて大きい。ピーク時とボトム時では、3倍ものボリュームの差がある。
季節変動の大きな多品種少量生産を可能にするために、滋賀製作所が生み出した生産方式が「変種変量生産」。最新の市場情報を日単位で生産計画に反映させ、需要変動に対応するフレキシブルな生産システムである。
たとえば、私が見学した室外機を担当するA1ラインは、1日に1440台を生産するが、その機種数は123機種。1個流しの混合生産が行われている。これだけのフレキシビリティを確保するには、それを支える仕組みと多能工の養成が不可欠である。
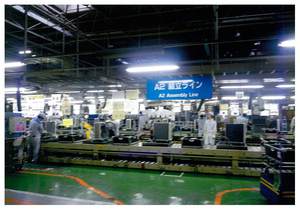
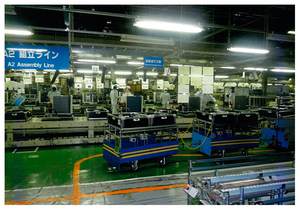
室外機の製造ライン
室内機の生産ラインは全部で4ライン。セルをラインの中に組み込んでいる。6人の作業者が11セルを担当している。ここでは、作業者に合わせて作業台の高さや角度がコンピューターで自動調整される仕組みが組み込まれている。日本人ならではのきめ細かい対応で、生産性と品質と短納期を確保する仕組みが、ここかしこに見られる。
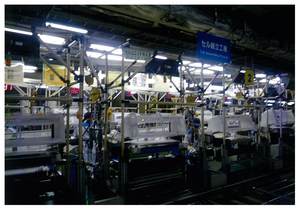
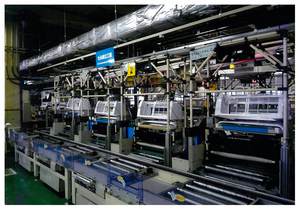
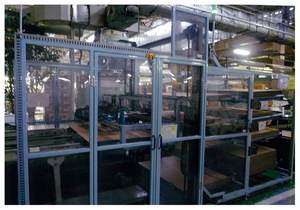
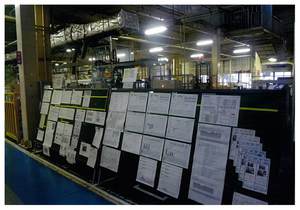
ダンボールの自動化ライン 見える化ボード
その一方で、人手に頼った方がフレキシビリティを確保できる工程は、作業者をサポートする仕組みを組み込む。一見何気ない生産ラインだが、実は人間の知恵とアイデアが高度に詰まった創意工夫溢れるラインなのである。
私が訪問した時、ちょうど提携先の中国・格力電器の技術者たちが、「変種変量生産」を学びに滋賀製作所を訪問していた。格力は美的電器と肩を並べる中国のエアコン2強の一角である。中国のエアコン市場は1億1千万台。日本のエアコン総市場が約700万台であるから、実に15倍以上の規模である。格力1社でなんと3550万台を生産し、近い将来5000万台を目指していると言う。桁違いの規模である。「体格」では勝負にならない。
しかし、彼らが現在生産しているのは、ボリュームゾーンの廉価品。画一的なロット生産を力づくで行うのは得意だが、フレキシビリティとは程遠い。格力も「規模の追求」だけでなく、「柔軟性の追求」にも目を向けているが、それほど簡単なことではない。
こんなエピソードを聞いた。「格力の技術者はすぐに"How"を聞きたがるが、"Why"は聞かない。すぐに役立つ答えを求めるが、その背景にある理屈を知ろうとはしない」。急成長を続け、目の前の市場を獲得することに奔走する中国メーカーにとっては、日本のモノづくりの本質指向はかえって邪魔なのかもしれない。
そして、より根本的には、「人」に対する思想や哲学がモノづくりの在り方を規定する。人を育て、ひとり一人の能力をいかに最大限に発揮させるかを考える日本的な考え方と、人を「駒」として扱い、ミスをすれば「罰金」を徴収する今の中国メーカーの考え方は、基本的には「水と油」である。その矛盾をクリアーしないと、滋賀製作所に根付いている改善提案制度やマイスターの育成には結びつかない。「体格」は資金と設備でなんとでもなるが、「体質」は人からしか生まれてこない。
滋賀製作所では長年に亘って改善活動に取り組み、現在でも月に3千件以上、1年に数万件の改善提案が出され、それらが生産性や品質の向上に結びついている。また、ダイキン全社で28名いる「マイスター」(機械部門の呼称、化学部門では「エキスパート」)の内、8名は滋賀製作所で勤務している。いくら形だけを真似ても、「人づくり」の思想が根付かなければ、「変種変量生産」を実現するのは難しい。
その一方で、ダイキンも大きな課題を抱えている。ダイキンは格力電器との業務提携以外に、2007年に買収したマレーシアのOYLインダストリーズ、その傘下にあった米国を拠点とするマッケイ・インターナショナルなどの生産拠点も抱えている。こうした拠点も含め、「地域で販売する商品は地域で生産する」という"地産地消"モデルを推進するダイキンの生産拠点は、全世界で49拠点にも及ぶ。
分散するこれらの生産拠点をどのように束ね、統治し、シナジーを追求していくのか。言語、文化、風習、制度が大きく異なるグローバル分散モデルを実現するのは、けっして容易なことではないが、日本のモノづくり企業が乗り越えなければならない大きな壁であることは間違いない。
そして、そのコントロールタワーとなるのが、マザーファクトリーである滋賀製作所である。商品開発機能を兼ね備える滋賀製作所が、さらなる進化を遂げた時に、日本のモノづくり企業の新たなお手本となるグローバルモデルが確立する。「体質」を誇る滋賀製作所であるが、さらなる高みの「体質」を目指そうとしている。