ビジネスの合理性を追求すれば、海外シフトは否定できない流れである。その中で、海外におけるモノづくりの実力を高め、その一方で日本におけるモノづくりの可能性を模索することが不可欠である。
そうした取り組みに先駆的に挑んできた企業がある。モーターサイクル、スクーターなどの二輪車を柱とするヤマハ発動機である。
2011年度の連結売上高は約1兆2800億円。二輪車はその内の7割を占める。舟艇(ボート)やボート用エンジンなどを手掛けるマリンは14%。その他にも、ATV(四輪バギー)やスノーモービル、ゴルフカー、産業用ロボットなども手掛けている。
同社は最もグローバルビジネスに成功している日本企業のひとつである。売上高に占める日本の割合は、わずか11%にすぎない。9割以上を海外で稼ぐ。中でも、アジアが全体の5割近くを占める。
創業者である川上源一氏は、「世界に通用しないものは商品ではない」と語り、当初から世界を意識したモノづくりを進めてきた。そのDNAは今でも脈々と受け継がれている。
中でも、二輪車の需要はアジアで急増している。2011年の世界の総需要は5735万台だが、その内中国が1400万台、中国・日本以外のアジアが3150万台を占める。世界の総需要のなんと約8割が中国を含むアジアである。日本の総需要はわずか44万台にすぎない。
こうした世界需要に対応するために、同社は「地産地消」を進めてきた。その結果、同社の生産拠点は全世界30ヶ国以上に広がっている。
しかしその一方で、日本におけるモノづくりの再編は思うように進んでいなかった。地元での雇用の問題、サプライヤーとの関係などもあり、輸出中心時代の生産拠点が数多くそのまま残り、非効率な生産体制が温存されていた。
そうした弱点にメスを入れるべく、2011年に国内の生産体制を抜本的に見直す構造改革に着手した。それまで国内12工場の25ユニットに分散していたものを、2011年末時点で10工場、18ユニットに集約させた。最終的には、7工場、14ユニットのスリムでコンパクトな体制へと収斂させる計画である。
こうした構造改革には必ず痛みが伴う。しかし、弱点をそのまま放置していては、熾烈なグローバル競争に勝ち残ることは困難である。強みを磨くことはもちろん大切だが、弱みを真正面から見据え、その克服に全力を挙げることがすべての日本企業に求められている。
同社の主力事業である二輪車も、その例外ではなかった。40万台(1直操業)あった国内の生産能力を、身の丈に合わせた20万台へと圧縮する必要があった。もし20万台を超える需要があっても、その時は2直操業すれば十分に対応できる。
身の丈を圧縮するために、統合前には二つの工場(エンジン工場、車体工場)に分散してものを、ひとつの工場に集約することを決断。担当する課・職場は10課・46職場から6課・21職場へと減った。
改革は統合・集約だけではない。モノのつくり方そのものを抜本的に見直す必要があった。
以前は、21本ものライン(エンジン12本、車体9本)で「乱流」生産していたものを、車種のタイプ別に6つのラインに集約した。エンジン・車体を統合的、一貫的に生産する「整流」生産へとシフトさせたのだ。
さらに、二輪車を生産規模・組み立て工数に応じて、3つのタイプに分類。生産台数が多く、組み立て工数が比較的少ないものは、「分業流れライン」。生産台数が少なくて、組み立て工数が比較的少ないものは、「セル生産」。そして、生産台数は少ないが、組み立て工数が多いものは「大型少量ショートライン」。商品特性に応じて、最も適切な生産ラインを選択している。
今回はその中の「セル生産」の現場を見学させてもらった。ここは月産400台以下の少量モデルを量産ラインから外し、2人で組み立てる。台湾向けの電動バイクなどを担当している。
この職場の最大の特徴は、担当する8人(4組)すべてが女性だということである。彼女たちは「セルガールズ」と呼ばれ、女性ならではの繊細さ、器用さを活かしたモノづくりを行っている。
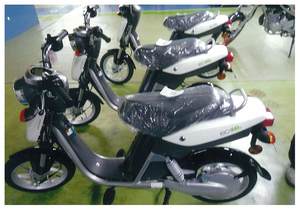
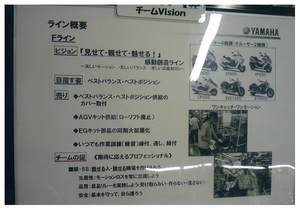
生産している小型バイク ラインの紹介パネル
ミニバイクの左右両側にひとりずつ立って、役割を分担。フレーム、モーター、ハンドル、ライトなど約100種類の部品を組み付けていく。工程の半分が終わったところで、左右の担当者が入れ替わる。1台当りの作業時間は約20分。量産ライン以上の生産性を確保している。
「セル生産」は"匠のライン"とも呼ばれている。作業者にはひときわ高い知識とスキルが求められる。同社には「匠認定制度」という社内基準があり、その資格を取得した者しかこのラインには入れない。
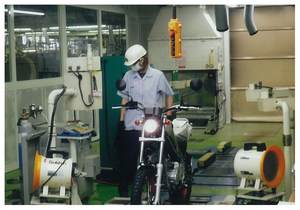
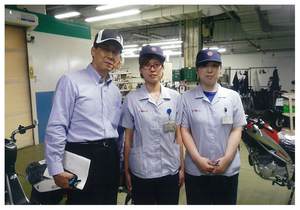
最終検査も女性 お話を伺った山田さんと大場さん
量を稼ぐラインではないが、この現場にはプライドと活気が溢れている。ヤマハ発動機が大切にしてきたモノづくりのスピリットが、このラインには受け継がれている。
海外で大きな工場を建て、設備を購入し、人を雇えば、とりあえずモノづくりは始められる。巨大で、最新鋭の海外工場が、量産モノづくりの柱となるのは、避けられない事実である。
しかし、日本のモノづくり企業が日本での生産にこだわり、なんとかモノづくりを残そうと努力するのは、けっして目先の経済合理性だけでは片づけられないものに目を向けているからである。
「セル生産」だけでなく、量産を担当する「分業流れライン」においても、Made in Japanのミッションがある。それは「世界標準」を定めるマザーラインとしての役割である。
付加価値を生む「価値作業」を定義し、理論値で作業工数を設定。世界に分散する組み立てラインの「標準」となっている。また、部品のキット化などの仕組みを工夫し、世界へ展開している。
実は、生産のグローバル化が進めば進むほど、「マザーファクトリー」としての日本のモノづくりの重要性は高まる。「量」ではなく、「質」を競うモノづくりにおいて、日本のモノづくり現場はこれからもなくてはならない存在である。そのためには、日本の現場は「知恵を生む現場」であり続けなくてはならない。